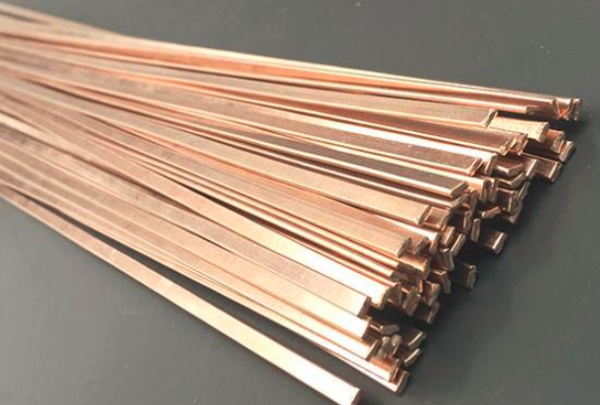
Is there any difference between phosphor copper electrode and silver copper electrode?What electrode is used for welding red copper and brass pipes?
There are differences in du between Bai bar and Silver copper bar in chemical composition and post-welding strength.
1, chemical zhi points are different
Phosphorus copper electrode is the composition of dao phosphorus, silver copper electrode is the chemical composition of silver.
2. Different strength after welding
Phosphor copper electrode after welding some brittle, silver copper electrode after welding strength is higher than phosphor copper electrode.
Classification and composition of phosphor copper electrode
1. BCu92P: component P: 7.5-8.5%; Copper: margin.The melting temperature is 710-750℃, the melting point is low, the flux is good, but more brittle, generally used for brazing no impact load, no vibration of copper and brass parts.
2. BCu93P (HL201/ BCUP-2) : component P: 6.80-7.50%; Copper: margin.The melting temperature is 710-793℃. The solder has good fluidity and can flow into the joints with small clearance, but the filler is brittle. It is generally used in the electromechanical and instrument industry for brazing copper and brass parts without impact load.
1. Welding sequence
In the use of copper welding rod welding to reduce deformation, welding seam length within 500 mm, can be used from one end of direct welding to the other end of the straight welding method, such as weld length greater than 500 mm, can be welded from the center to both ends, welding carbon steel to take some of the deformation prevention methods, can be used in the welding of copper.
2. Welding current and electrode diameter
The diameter and welding current of the copper electrode are selected according to the thickness of the electrode, the beginning of the welding seam, the outer profile of the welding electrode and the heat dissipation conditions, etc. Generally, the welding current is 40-50 times of the diameter of the electrode.